Керамзитобетонные блоки своими руками
|
|
Semsey | Дата: Пятница, 12.04.2013, 12:01 | Сообщение # 1 |
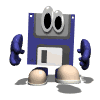 Admin
Группа: Администраторы
Сообщений: 309
Статус: Offline
| Керамзитобетонные блоки
Керамзитобетонные блоки - стеновые легкие блоки, имеющие стандартные размеры 190х190х390мм. Блоки изготавливают путем объемного вибропрессования из керамзитобетонной смеси, в идеале состоящей из керамзитового песка, самого керамзита и цемента.
По экологичности керамзитобетонные блоки можно сопоставить на один уровень с керамическим кирпичом, так как при производстве блоков используются натуральные природные материалы. Имеются конечно и минусы при использовании керамзитобетонных блоков в строительстве: блоки из керамзитобетона более хрупкие, нежели кирпич, имеют пористую структуру, что незначительно снижает их прочность и морозоустойчивость(количество циклов замерзания - оттаивания на открытом воздухе). Но, несмотря на подобные недостатки, использование керамзитобетонных блоков остается одним из выгодных решений для строительства малоэтажных зданий. Например, можно построить 2х-3х этажный коттедж и использовать железобетонные плиты перекрытия между этажами. К тому же, себестоимость строительных работ, по сравнению с применением простого кирпича, снижается процентов на 30. А если еще и научиться производить этот стеновой материал самому - выгода будет довольно ощутимой.
Для повышения прочности используют кварцевый, либо обогащенный песок
Для того, чтобы блоки получились более прочными, нужно все-таки использовать смесь с обогащенным песком, тогда на стены из керамзитобетонных блоков можно будет положить железобетонные плиты перекрытия. Блоки же из смеси с керамзитовым песком можно будет применить в перегородках не несущих большую нагрузку.
Зачастую производители керамзитобетонных блоков хотят значительно сэкономить на их себестоимости, это : низкое содержание керамзита, из-за чего теплопроводность сводится к теплопроводности простого бетона; использование вместо обогащенного песка обычного речного и даже карьерного, что влияет на прочность и внешний вид блоков; низкое содержание цемента, что также отражается на прочности готового изделия. Также некоторые "торопыги" сушат только что отформованные блоки тепловыми пушками - это вообще недопустимо, так как цемент, вместо того чтобы набрать прочность, попросту высыхает и рассыпается. Действительно качественные блоки из керамзитобетона производятся только на крупных специализированных заводах, которых не так уж и много в стране. Если встает вопрос о покупке - лучше заплатить дороже за качественный товар, нежели брать неизвестно что не знамо из чего слепленное. Вполне можно сделать керамзитоблоки своими силами. Это значительная экономия средств, производство непосредственно на стройплощадке, и самое главное, Вы будете знать как и из чего сделаны Ваши блоки.
Сегодня не проблема приобрести бетономешалку (без нее не обойтись) и вибростанок для производства стеновых блоков, но также можно сделать его своими руками - этому посвящена отдельная страничка. Сразу хочу предупредить. Не "ведитесь" что производитель станка заявляет 300, 500 штук в день для бригады из двух человек. Это было бы реально если бы еще одна бригада делала и подносила раствор, да и физически это нелегко, поэтому рассчитывайте штук на 120 - 150. Если Вы уверены в себе, своих силах, то думаю стоит попробовать, ведь стоимость готового керамзитобетонного блока снизится в разы. Так что, дерзайте.
Успешный предприниматель - не тот, кто все знает, а тот, который быстро учится.
|
|
| |
Semsey | Дата: Пятница, 12.04.2013, 12:09 | Сообщение # 2 |
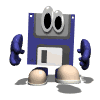 Admin
Группа: Администраторы
Сообщений: 309
Статус: Offline
| Почему керамзитобетон
Многие застройщики задаются вопросом, какой же материал выбрать для возведения стен своего будущего дома? В настоящее время выбор подобных стеновых материалов весьма разнообразен, и выбрать для себя наиболее подходящий – не всегда легко. Рассмотрим четыре вида самого востребованного на сегодняшний день стенового материала.
Кирпич.
Кирпич, безусловно, занимает лидирующие позиции. Это прочный и долговечный стеновой материал, основными компонентами которого являются глина и песок. После формования, кирпич проходит обжиг, что делает из песчано-глиняной смеси прочную обожженную керамику.
Прочность кирпича составляет от 50 до 150 кг/кв.см (в зависимости от марки), что вполне достаточно для возведения несущих стен даже в многоэтажных домах, не говоря уже о постройке частного, двух – трех этажного дома.
Морозостойкость кирпича составляет 50 циклов.
Теплопроводность – 0.3-0.8 Вт/мГрад.
Влагопоглощение кирпича составляет 40%.
Кирпич является безусадочным материалом, что вполне позволяет его использовать для облицовки фасадов.
Имеется только один незначительный недостаток – вес кирпича, который составляет 1500 – 2000 кг/куб.м. Этот недостаток легко исправить, рассчитав и заложив соответствующий фундамент.
Керамзитобетонный блок.
Прочность керамзитобетона – от 50 до 150 кг/кв.см.
Морозостойкость – 50 циклов.
Теплопроводность – 0.15-0.45 Вт/мГрад .
Влагопоглощение керамзитобетона – 50%.
Керамзитобетонный блок также не дает усадку, как и кирпич.
Вес керамзитобетона – от 700 до 1500 кг/куб.м.
Пеноблок.
Это стеновой материал, для производства которого используется цемент, песок и пенообразующее вещество. Представляет из себя пористый бетонный блок, укладывается либо на цементно – песчаный раствор, либо на специальный клеящий состав. Из-за своей сравнительно небольшой прочности подходит только для малоэтажного строительства.
Прочность пенобетона – от 10 до 50 кг/кв.см.
Морозостойкость – 25 циклов.
Теплопроводность – 0.2-0.4 Вт/мГрад.
Влагопоглощение – 95%.
Данный материал дает усадку, порядка 0.6-1.2 мм/м.
Вес пенобетона – 450-900 кг/куб.м.
Газосиликатные блоки.
Стеновой материал, состоящий из силикатного связующего вещества, песка и пенообразующего компонента. Технология производства сходна с технологией производства пенобетона. Используется только для возведения перегородок и стен, не несущих нагрузку.
Прочность – от 5 до 20 кг/кв.см.
Морозостойкость – 10 циклов.
Теплопроводность – 0.15-0.3 Вт/мГрад.
Влагопоглощение – 99%.
Газосиликатные блоки также подвержены усадке, которая может составлять 1.5 мм/м.
Вес – 200-600 кг/куб.м.
Исходя из перечисленных выше параметров, керамзитобетонный блок, на мой взгляд, имеет довольно неплохие качества для того, чтобы использовать его для возведения стен. Имея почти такую же прочность, как и кирпич, керамзитобетонный блок значительно легче и имеет меньшую теплопроводность. Превосходство керамзитобетона по всем параметрам над пенобетоном и газосиликатом, делает его действительно универсальным материалом. В Европе, например, доля строительства домов из керамзитобетонных блоков превышает 50% от общего объема, так как считается более оптимальным материалом для возведения стен. Кирпич же, из-за своей внешней презентабельности, нередко используется как материал для облицовки стен из керамзитобетонных блоков.
Успешный предприниматель - не тот, кто все знает, а тот, который быстро учится.
|
|
| |
Semsey | Дата: Пятница, 12.04.2013, 12:47 | Сообщение # 3 |
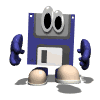 Admin
Группа: Администраторы
Сообщений: 309
Статус: Offline
| Состав керамзитобетона
Для замешивания керамзитобетонной смеси понадобится бетоносмеситель объемом не менее 130л и емкость(корыто) для готовой смеси литров на 70 - 100. Для приготовления раствора нам понадобится керамзит фракции 5-10, обогащенный песок, цемент, пластификатор(можно использовать обычное средство для мытья посуды), вода. Соотношение компонентов на 130литровую бетономешалку : вода 5л, цемент 8л, пластификатор по инструкции к нему(если жидкое мыло - то 60-70 грамм), обогащенный песок 30л, керамзит фракции 5-10 30л.
Порядок загрузки компонентов таков. Сначала наливаем воду, включаем, добавляем пластификатор, высыпаем цемент, затем песок, тщательно перемешиваем, только после этого добавляем керамзит и продолжаем перемешивать до тех пор, пока гранулы керамзита не покроются цементным раствором. Выключаем, высыпаем смесь в корыто. На все операции примерно уходит минут 7. Готовая смесь не должна рассыпаться и не должна быть мокрой. Если получается слишком сухая смесь, то нужно добавлять воду еще в процессе перемешивания в небольших количествах. Если же получился мокрый раствор - нужно просто дать ему немного постоять, он слегка "схватится" и станет нужной консистенции. На стандартную форму для блока уходит в среднем 10 - 11 литров смеси(ведро). Блоки можно формовать как на индивидуальных поддонах, так и на ровном бетонном основании(плита, бетонный пол, даже отмостка).
Преимущество формования на индивидуальных поддонах - можно сразу же переносить готовые блоки в другое место для складирования, а через несколько часов на них сверху можно ставить еще поддоны с блоками, не более 3х рядов. Поддоны делают примерно на 50-100 мм больше размеров самого блока так, чтобы можно было аккуратно взять поддон за края с уже стоящим на нем блоком и перенести его. Если на улице, или в помещении где находятся блоки, тепло, можно укладывать их в штабеля уже через 24-36 часов, не более 5-ти рядов в высоту.
Последним этапом будет сушка блоков. Для полного застывания достаточно и двух дней, но желательно, дать блоку дополнительную неделю на открытом воздухе под навесом. Летом в жару, при сильном пересыхании блоков, нужно поливать их водой. Желательно не давать им полностью высохнуть в течении недели - двух. Если же уже через 3 - 5 дней после изготовления использовать блоки в кладке, процесс постоянного увлажнения можно и опустить, так как в стене они будут сохнуть дольше, что в принципе и требуется. Вообще, цемент в готовых изделиях марочную прочность набирает в течении 30-ти дней при постоянном увлажнении изделия.
Успешный предприниматель - не тот, кто все знает, а тот, который быстро учится.
|
|
| |
Semsey | Дата: Пятница, 12.04.2013, 12:51 | Сообщение # 4 |
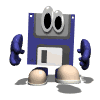 Admin
Группа: Администраторы
Сообщений: 309
Статус: Offline
| Пропаренные керамзитобетонные блоки
Бытует мнение, что пропаренные керамзитобетонные блоки гораздо прочнее, чем блоки естественной сушки. На самом деле – это не совсем так. Пропаривание керамзитобетонных блоков, как и других изделий на цементном связующем, конечно же, увеличивает их прочность, не на много, конечно, но все-таки, но это не основная цель процесса пропаривания.
В результате обработки паром, изделия (блоки, ж/б плиты, перемычки и т.д.) схватываются и набирают марочную прочность практически за несколько часов, после чего их уверенно можно укладывать в штабеля, а еще через некоторое время, после просушки, складировать на открытом воздухе или отправлять на отгрузку. Пропаренные бетонные изделия, в отличие от изделий из бетона естественной сушки, можно практически сразу использовать по их прямому назначению – использовать в строительстве.
Не пропаренные керамзитобетонные блоки набирают марочную прочность на протяжении 28 дней, как и любые бетонные и железобетонные изделия. При довольно крупном производстве, когда каждый день нужны большие партии блоков, мало их просто отформовать, нужно еще где-то их разместить для того, чтобы они постепенно высыхали (с периодическим их увлажнением) и набирали прочность. Понятно, что для естественной сушки потребуются просто огромные площади, а если блоки производятся для их последующего сбыта, что тогда? Покупатель ведь не будет заказывать блоки за 28 дней до приобретения, да и производителю будет накладно содержать огромные склады не совсем готовой продукции. Процесс пропаривания в этом случае будет самым выгодным решением для обеих сторон. Потенциальному покупателю не нужно будет долго ожидать заказанной продукции, а производитель сможет обеспечить наличие этой продукции в кратчайшие сроки, 1-2 суток, причем без занимания огромных площадей для сушки блоков.
Пропаривание бетона, в данном случае – керамзитобетона, технологически сложный и ответственный процесс, который требует определенных затрат - необходимо будет установить теплоизолированную камеру нужных размеров, приобрести промышленный парогенератор и соответственно нанять грамотных людей для обслуживания этого хозяйства.
Соблюдение технологии влажно тепловой обработки обязательно, но многие предприниматели, занимающиеся производством керамзитобетонных блоков, почему-то пренебрегают этими технологиями, недодерживая блоки в паровых камерах, из-за чего блоки просто высыхают, так и не набрав должной прочности. Виной всему, в подобных случаях, является жадность – увеличение оборота продукции с минимальными затратами, а какого качества будет подобная «скоросделанная» продукция – это уже другой вопрос.
Керамзитобетонные блоки, пропаренные и высушенные надлежащим образом, производятся преимущественно на крупных заводах, дорожащих своей репутацией и качеством выпускаемой продукции. Если встает вопрос о приобретении керамзитобетонных блоков, то стоит рассмотреть предложения именно крупных производителей, хотя и цена на блоки может оказаться несколько выше, чем у многих частников.
Успешный предприниматель - не тот, кто все знает, а тот, который быстро учится.
|
|
| |
Semsey | Дата: Пятница, 12.04.2013, 12:59 | Сообщение # 5 |
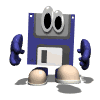 Admin
Группа: Администраторы
Сообщений: 309
Статус: Offline
| Как сделать форму
Для самостоятельного производства блоков нам прежде всего понадобится форма для их изготовления. Подобную форму(вибропрессовочный станок или вибростол с одной или несколькими формами для блоков) можно купить, а можно изготовить своими руками. Ниже постараюсь подробно описать как это делается и что для этого нужно.
Нам потребуется лист металла толщиной 5мм для стенок самой формы. Более тонкий металл лучше не использовать, так как при вибропрессовании стенки формы будет просто распирать и блоки будут получаться слегка округлыми, что недопустимо. Также нужен будет лист металла толщиной 3мм для пустотообразователей. Пустоты в керамзитобетонных блоках не только экономят 25-30% раствора, они необходимы для создания воздушных колодцев внутри уже готовой стены, что способствует значительному снижению теплопроводимости стен.
Для работы непосредственно с металлом нужны будут : УШМ(болгарка) с диаметром диска 115-125мм (230мм лучше не использовать), сварочный аппарат (или знакомый сварщик который действительно может сварить то, что требуется), крупная и мелкая наждачная бумага и дрель со сверлом по металлу. Ну и конечно же Ваше желание и умелые руки.
Убедительная просьба ! С УШМ работать нужно крайне осторожно, так как это очень и очень травмоопасный инструмент. Всегда надежно закрепляйте заготовки в тисках, при работе держите электроинструмент надлежащим образом, согласно правилам экплуатации указанным в техпаспорте инструмента, соблюдайте порядок и чистоту на рабочем месте. Это не просто слова или цитаты из правил техники безопасности - это действительно необходимо !
Итак, приступим. Для начала нужно разметить лист металла толщиной 5мм так, чтобы получилось два прямоугольника со сторонами 260х386х260х390мм (рис 1).
Не совсем прямоугольники, скорее - трапеции, но это необходимо для того чтобы придать форме совсем небольшую конусность. Нужно это для того, чтобы форма легче снималась уже с готового, отформованного блока. Пустотообразователи для формы также выполняются в форме конуса, но об этом чуть позже. Внимание ! Диагонали этих прямоугольников должны быть равны, а размеры сторон должны соответствовать указанным выше размерам, иначе форма получится кривой. Также размечаем еще два прямоугольника со сторонами 260х196х260х200мм (рис 2).
Вырезаем, проверяем размеры.Точно с середины стороны 196мм делаем пропил толщиной 4мм и длиной 70мм перпендикулярно этой стороне. Затем собираем все четыре заготовки таким образом, чтобы те стороны, которые короче противоположных на 4мм оказались сверху. Сложить листы так, как показано на рисунке 3.
Получаем примерно следующую конструкцию (рис 4).
Провариваем нашу будущую форму по получившимся вертикальным ребрам но Только с наружной стороны. Проваривать металл нужно аккуратно, так, чтобы швы с внутренней стороны формы оставались чистыми.
Успешный предприниматель - не тот, кто все знает, а тот, который быстро учится.
|
|
| |
Semsey | Дата: Пятница, 12.04.2013, 13:03 | Сообщение # 6 |
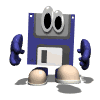 Admin
Группа: Администраторы
Сообщений: 309
Статус: Offline
| Пустотообразователь
Для пустотообразователя нам понадобится листовой металл толщиной 3мм (можно и 2,5мм), а также полоска 5мм металла длиной 480мм и шириной 35мм - она нужна для того, чтобы собрать три пустотообразователя вместе и закрепить их на стенках формы.
Размечаем лист металла как указано на рисунке 5.
По вертикальным наклонным линиям делаем болгаркой канавки на половину толщины листа металла (рис 6).
Отрезаем два угла, сгибаем по пропилам. Должна получиться усеченная пирамида (рис 8). Затем нужно выровнять стороны, где в сечении получились прямоугольники. Отрезаем верх и низ этой усеченной пирамиды так, чтобы высота ее составила 230 мм (рис 7).
Получится всего один вертикальный шов, который нужно будет прижать и проварить с внутренней стороны. Нам нужно будет три таких пустотообразователя. Затем нужно будет вырезать дно и крышку на каждый. Донышко должно заходить внутрь прямоугольника образованного сторонами 90мм и 55мм. Размер его примерно составит 87х52мм, но лучше будет еще раз замерить конкретно по внутренним сторонам меньшего прямоугольного отверстия пустотообразователя. Приваривать донышко нужно также изнутри. Крышки же, в отличии от донышек, должны быть замерены по наружным сторонам большего прямоугольного отверстия. Примерный размер – 110х75мм (рис 9,10).
Успешный предприниматель - не тот, кто все знает, а тот, который быстро учится.
|
|
| |
Semsey | Дата: Пятница, 12.04.2013, 13:08 | Сообщение # 7 |
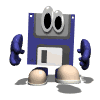 Admin
Группа: Администраторы
Сообщений: 309
Статус: Offline
| Продолжение
Вырезаем крышки и пока откладываем их в сторону. Теперь нужно сделать пропилы в верхних стенках каждого пустотообразователя. Пропилы делаются точно посередине каждой стороны 110мм длиной 55мм и шириной 5мм (рис 11).
Затем берем полоску 5мм металла длиной 480мм и шириной 55мм. От краев полоски отступаем на 42мм и делаем пропилы глубиной 1.1-1.2мм. Вставляем ее в прорези пустотообразователей как показано на рисунке 12.
Привариваем каждый пустотообразователь к этой полоске опять же с внутренней стороны. Самое главное – это чтобы каждый пустотообразователь конусом "смотрел” строго вниз относительно привариваемой полоски. После этого можно приваривать крышки на пустотообразователи. Приваривать придется с наружной стороны. Нужно постараться сделать швы поаккуратнее. Получиться должна будет примерно такая конструкция (фото внизу).
Успешный предприниматель - не тот, кто все знает, а тот, который быстро учится.
|
|
| |
Semsey | Дата: Пятница, 12.04.2013, 13:12 | Сообщение # 8 |
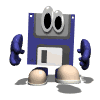 Admin
Группа: Администраторы
Сообщений: 309
Статус: Offline
| Теперь займемся площадкой для керамзитобетонной смеси. Ее можно сделать из металла толщиной 3 мм. Вырезаем полоски металла как показано на рисунке 13.
Прямоугольники со сторонами 396х100мм послужат непосредственно самой площадкой для раствора, остальные полоски - бортиками для этой площадки. Все это нужно будет приварить на форму как показано на рисунке 14.
После того, как площадка будет приварена, нужно будет прорезать два противоположных бортика, продолжив прорези сделанные в торцах формы (для того, чтобы вставить пустотообразователь). Затем нужно будет приварить уголки из металла толщиной 3-5мм к прорезям в самой форме. После этого, вставить пустотообразователь в форму и просверлить сквозные отверстия диаметром 8мм сквозь уголок и часть планки пустотообразователя, выходящей за пределы формы. Подробно на рисунке 15.
Через эти отверстия пустотообразователь будет крепиться болтами к форме. Остается только приварить к форме ручки и сделать крышку. Ручки приваривать нужно непосредствено к самой форме, но так, чтобы они не препятствовали пустотообразователю свободно выниматься из формы.
Успешный предприниматель - не тот, кто все знает, а тот, который быстро учится.
|
|
| |
Semsey | Дата: Пятница, 12.04.2013, 13:15 | Сообщение # 9 |
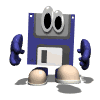 Admin
Группа: Администраторы
Сообщений: 309
Статус: Offline
| Крышка для формы
Итак, когда форма готова, нужно сделать крышку для нее. Крышку нужно делать из металла, толщиной не меньше 5мм, она должна быть достаточно прочно и надежно сварена, чтобы выдерживать вибрацию, передающуюся от перфоратора.
Вырезаем прямоугольный лист металла размерами 384х184мм. Получившийся лист должен свободно заходить в форму слегка, или вообще не касаясь стенок. Далее нужно будет вырезать прямоугольные отверстия под пустотообразователи. Разметку отверстий нужно проводить по месту, предварительно опустив в форму пустотообразователь и положив на него сверху наш вырезанный прямоугольник, затем с нижней стороны формы нужно будет разметить будущую крышку, тщательно очертив карандашом верх каждого пустотообразователя, прилегающего вплотную к прямоугольнику. Линии нужно будет прочертить и там, где будет проходить планка, соединяющая пустотообразователи. Получим примерно следующее.
Вырезаем прямоугольники внутри листа и проверяем соответствие размеров. Линии, размеченные между внутренними прямоугольниками, пока не трогаем. Крышка должна опускаться свободно, не задевая (или слегка касаясь) стенок формы и пустотообразователи. Для усиления конструкции, вдоль сторон 384мм привариваем уголки, но так, чтобы они не заходили ни за край листа, ни за внутренние линии разметки.
Затем нам понадобятся две пластины из металла толщиной 7-10мм размером 150х90мм, которые нужно будет приварить к внутренним сторонам уголков - они будут служить опорой под площадку, которая будет передавать вибрацию.
Пластины нужно приваривать так, чтобы середина стороны пластины совпадала с серединой стороны крышки. Теперь нужно вырезать пластину для площадки под перфоратор, лучше - две пластины толщиной 5-7 мм каждая, размерами 120х90 мм. Приварить сначала одну пластину к получившимся опорам, затем уже к ней приварить вторую пластину по периметру. В центре получившейся площадки приварить обычную шайбу (чем толще - тем лучше) - чтобы бур перфоратора бил в центр и не соскальзывал с площадки. После этого к опорам под площадку привариваем два прутка диаметром 16мм и длиной 230-240мм так, чтобы в итоге от низа приваренного прутка до самого низа крышки получилось расстояние 70мм, - это будут ограничители крышки. Середины прутков ориентируем на центр площадки.
Успешный предприниматель - не тот, кто все знает, а тот, который быстро учится.
|
|
| |
Semsey | Дата: Пятница, 12.04.2013, 18:38 | Сообщение # 10 |
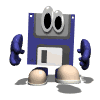 Admin
Группа: Администраторы
Сообщений: 309
Статус: Offline
| Как выбрать вибростанок
Для начала – нужно определиться, для каких собственно целей нужен станок по производству керамзитобетонных блоков. Если нужно построить дом, гараж и баню – вполне хватит одноматричного вибростанка (на один блок) типа “блокмастер”. Стоимость его на официальном сайте производителя составляет 10 000 рублей. Станок довольно прост в эксплуатации и вполне надежен, его ресурса должно хватить, как минимум на изготовление 10 тысяч блоков. Кстати, конструкцию своей формы я частично позаимствовал именно у такой модели. Одноматричные станки под брендом “вибромастер - гермес” почему то не внушают доверия уже на видео о работе станка, размещенное на сайте этого производителя – сама форма выполнена из очень тонкого металла и при ее снятии с блока, последний, просто растрескивается пополам по горизонтальной плоскости. И все это крупным планом на оф. Сайте … Я никак не хочу сделать тем самым рекламу, просто, даже если не брать в расчет мой опыт использования этих моделей, существует множество отзывов в сети по тем и другим станкам, где “блокмастер ” не на последнем месте.
Если же у Вас появилось желание заняться производством керамзитобетонных блоков в больших объемах – понадобится уже двух-, трех-, или четырех-матричный вибростанок, или же вибростол на две, четыре или шесть форм для блоков. Если производство планируется сравнительно небольшими партиями, по 1000-2000 штук в смену, можно приобрести и одноматричный станок, но только промышленного типа. Такие модели обычно очень дороги, но и вполне надежны.
У вибропрессовочного станка существует некоторое преимущество, по сравнению с вибростолом. При запрессовке блока с помощью прессовочного станка, давление на керамзитобетонную смесь происходит одновременно с вибрацией, результат – более быстрая запрессовка, даже при использовании одноматричного станка, и хорошая первоначальная прочность блока. Вибростол же, не столько хорош в изготовлении блоков, сколько для производства брусчатки и тротуарной плитки, если его, конечно, укомплектовать соответствующими формами.
Если будете приобретать какой-либо станок у диллеров, или непосредственно на заводе-изготовителе – не постесняйтесь потребовать проверки работоспособности именно того станка, который Вы собрались приобрести. На заводе эта услуга предоставлялась. Пусть на этом станке отформуют парочку блоков прямо в Вашем присутствии. Если вдруг, блок застрянет в форме, или же сорвет углы у блока – не ведитесь на отговорки по поводу “новизны” и ”непритертости” формы, такого быть просто не должно. Форма, конечно, может первое время сниматься чуть туговато, но она должна все-таки сниматься с блока, а не ломать его. Не нужно брать вибростанок, форму которого нужно разбирать, чтобы достать из нее блок. С такой формой Вы не только потеряете время, от частых разбираний – собираний форма быстро придет в негодность. Корпус формы должен быть цельным, а вот пустотообразователь наоборот - должен быть съемным.
Нужно только учесть, что для производства больших объемов данной продукции Вам понадобятся большие площади не только для ее производства и хранения, а также и для складирования сырья для производства блоков.
Успешный предприниматель - не тот, кто все знает, а тот, который быстро учится.
|
|
| |
Semsey | Дата: Пятница, 12.04.2013, 18:44 | Сообщение # 11 |
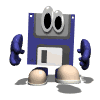 Admin
Группа: Администраторы
Сообщений: 309
Статус: Offline
| Типы вибростанков
Виброформовочные станки для производства стеновых блоков на цементном связующем можно поделить на четыре типа.
Ручные малогабаритные одно или двух матричные станки. Оснащаются электровибратором, который крепится непосредственно к корпусу станка, и съемными или несъемными пустотообразователями.
Вибрация передается через стенки формы непосредственно в тело блока, что делает процесс формования более быстрым и качественным. Станки предназначены для виброформования стеновых блоков поддонным и безподдонным методом. При съемном пустотообразователе можно производить как пустотные, так и полнотелые блоки. Загрузка смеси ручная. Процесс формования блока также происходит вручную, при вдавливании верхней прижимной планки (пуансона). Форма с блока снимается и переставляется вручную.
Достоинства станков данного типа в том, что они сравнительно недороги (порядка 10 000 рублей), имеют небольшие габариты, подключаются к бытовой электросети напряжением в 220 вольт и вполне просты и надежны в работе.
Недостатки – много ручного труда, не подходят для производства больших партий блоков.
Производительность таких станков варьируется от 200 до 600 блоков в смену.
Передвижные механизированные станки являются чуть более сложной конструкцией, точнее они оснащены рычажным механизмом для снятия формы с блока и колесиками для передвижения станка по ровной горизонтальной поверхности. Более «продвинутые» модели имеют также рычажную систему для вдавливания верхней прижимной планки. Вибратор крепится к стенке формы. Станки такого типа могут иметь до четырех матриц (форм), что позволяет формовать до четырех блоков одновременно.
Вибрация, как и у предыдущего типа станков, передается в тело блока через стенки формы. Загрузка формовочной смеси, как и формование, происходит точно также, как и на ручном переносном станке, единственное существенное отличие - облегчен процесс разгрузки формы.
Достоинства. Станки передвижного типа более удобны в работе, имеют лучшую производительность и снижают трудозатраты за счет механической разгрузки формы.
Недостатки – большие габариты и более сложная конструкция, вследствие чего - большая цена (от 16 000 рублей).
Производительность передвижных станков может достигать 1500 блоков в смену, но это при наличии двух и более матриц, а также, при работе 3х – 5ти человек.
Вибростол. Имеет значительные конструктивные особенности от станков предыдущих типов. Блоки формуются исключительно на индивидуальные поддоны, которые выполняются из листового металла толщиной 2 – 3 мм. Поддоны размещаются непосредственно на поверхности вибростола, затем, на эти поддоны устанавливаются металлические формы с пустотообразователями. Загрузка формовочной смеси производится вручную. Снимают отформованные блоки вместе с формой и поддоном, переносят в таком виде к месту сушки, ставят вместе с поддоном на стеллаж, вытягивают поддон, только затем снимают форму. Вибростолы могут быть рассчитаны на одну, две, три и даже шесть форм, что позволяет формовать одновременно до шести блоков.
Вибрация передается в тело блока не напрямую, но тоже довольно эффективно, поскольку устанавливаемый внизу вибростола электровибратор, обеспечивает вертикальное направление передачи вибрации. Немного усложнен процесс разгрузки форм, но, некоторым этот способ может показаться более удобным в связи с тем, что готовые блоки сразу можно переносить к месту сушки.
Достоинства вибростолов в том, что обеспечивается хорошая плотность блоков, а также удобство размещения готовой продукции.
Недостатки такого устройства также очевидны: немалые габариты и большой вес станка; сравнительно высокая стоимость; много ручного труда.
Производительность вибростола зависит и от его размеров и от количества форм, к примеру, для вибростола размером под три формы понадобятся как минимум шесть форм для блоков. В среднем, производительность варьируется от 250 до 1300 блоков в смену.
Вибропрессы – это самые «серьезные» станки для производства блоков. Они оснащены гидроприводом, который во время вибропрессования давит на блок сверху с силой в несколько тонн. Пустотообразователи крепятся к пуансону, который и вдавливается в тело блока при формовании. Расформовка происходит автоматически, при использовании того же гидропривода. Блоки формуются на индивидуальных поддонах. Используются такие станки для промышленного производства блоков.
Вибрация, как правило, передается в тело блока напрямую, от основания формы. Если учесть еще дополнительную силу сжатия, то получается довольно плотный и прочный стеновой материал.
Достоинства вибропресса очевидны: даже одноматричный вибропресс имеет очень большую производительность; высокая плотность производимого материала (блоков); ручной труд практически исключен – вручную происходит только загрузка формовочной смеси и выгрузка готовых блоков.
К недостаткам можно отнести только большие размеры и вес станка, а также его высокую стоимость – от 180 000 рублей.
Производительность вибропрессов начинается от 1000 штук в смену.
Успешный предприниматель - не тот, кто все знает, а тот, который быстро учится.
|
|
| |
Semsey | Дата: Среда, 17.04.2013, 17:08 | Сообщение # 12 |
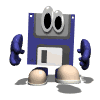 Admin
Группа: Администраторы
Сообщений: 309
Статус: Offline
| Формование блоков
Хочу рассказать о самом процессе формования керамзитоблоков. Для этого понадобятся: бетоносмеситель объемом не менее 130л; несколько десятилитровых ведер (не меньше двух); емкость на 120-180 литров (корыто прямоугольной формы с высокими бортами) под готовый керамзитобетонный раствор; две совковые лопаты (одна для песка, другая для керамзитобетона); кельма (мастерок) с формой подошвы в виде усеченной пирамиды (можно прямоугольный), ну и конечно же сам станок для изготовления блоков и свободная площадка для их формования.
Из компонентов нужны будут: обогащенный песок (фактически то же, что и ПГС, только без камушков, кто продает подобные вещи – тот знает, что нужно будет Вам привезти); керамзит фракции 5-10 (возят обычно минимум по 10 кубов – мне хватило на 3000 блоков); цемент 400 марки; самое дешевое средство для мытья посуды; вода и запасная пара рук, можно без головы.
Самое главное при замешивании смеси – не переусердствовать с количеством воды и жидкого мыла и соблюдать очередность загрузки компонентов в бетономешалку.
Так как обычная, бытовая электрическая бетономешалка не предназначена для замешивания легких бетонов (на крупном производстве керамзитоблоков используют только инерционные бетоносмесители), нужно ее либо доработать, сделав дополнительно прорезь для фиксатора, либо держать руками под таким углом, чтобы смесь хорошо перемешивалась и в то же время не высыпалась из нее. Это не сложно – почувствуете в процессе работы.
1. Заливаем воду в бетоносмеситель, включаем его.
2. Добавляем примерно 50 мл жидкого мыла.
3. Высыпаем цемент.
4. Засыпаем обогащенный песок, только не весь сразу, а по половине ведра с небольшими интервалами, чтобы каждая добавленная порция успевала немного перемешаться с основной массой. Не пугайтесь, что получается почти сухая масса.
5. Тщательно перемешиваем раствор, наклонив бетономешалку на необходимый угол наклона. Не добавляйте воду, если раствор покажется Вам сухим – он за считанные минуты становится мокрым в процессе перемешивания.
6. Добавляем керамзит, тоже не весь сразу, а по ведру, с небольшим интервалом. Перемешиваем так, чтобы каждый шарик керамзита покрылся серой цементной пленкой.
7. Выключаем, выгружаем смесь в корыто.
Процесс замешивания занимает примерно 7 минут. Если с первого раза не получится – ничего страшного, раствор Вы не испортите.
8. Обязательно вычищаем остатки раствора со стенок бетономешалки. Если этого не сделать – при следующем замесе раствор будет жутко прилипать к стенкам бетономешалки, что сильно затруднит перемешивание.
Если пользоваться станком типа “блокмастер”, понадобится площадка с ровным основанием, вполне подойдет и бетонный пол строящегося дома. Перед формованием блоков пол лучше застелить бумагой – я использовал пустые мешки из-под цемента. На площади в 12 квадратных метров вполне можно будет разместить 100 блоков. Если же подходящей площадки под блоки не нашлось, можно формовать блоки на индивидуальных поддонах. Не делайте ошибки – не формуйте несколько блоков на одном большом поддоне. Вибрация, при которой будет запрессовываться следующий блок, просто разрушит уже отформованные блоки, находящиеся на этом же поддоне. На бетонном основании такого не происходит, так как вибрация в значительной мере погашается, точнее – не передается как по дереву. Именно поэтому для каждого блока и нужен индивидуальный поддон.
Нагружаем керамзитобетонный раствор в ведро, переносим на площадку, к месту формования блоков. Располагаем форму так, чтобы начать формовать ряды с левого дальнего угла площадки. Перед тем, как поставить форму на место формования блока, нужно на это самое место кельмой положить немного керамзитобетонного раствора – на дно будущего блока. Процедура эта необязательная, просто на некоторых станках при формовании раствор может не заходить под низ пустотообразователей. Последствия – пустоты в блоке получатся сквозные. В принципе, ничего страшного в этом нет, просто при кладке таких “дырявых” блоков кладочный раствор будет проваливаться в эти отверстия.
Засыпаем керамзитобетонную смесь в форму, прижимаем крышкой и включаем вибратор. Процесс вибропрессования длится около 20 ти секунд, пока крышка формы не просядет по ограничители.
Выключаем вибратор. Снимаем крышку и поднимаем форму – блок готов. Если форма не снимается с блока – слегка постучите по наружным стенкам формы деревянным молотком, затем снимайте. Форма должна сниматься не совсем легко, но она не должна ломать блок. Если срывает верхние углы – скорее всего причина в слишком сухом растворе. Формование следующего блока нужно проводить вплотную к предыдущему, оставив зазор для свободного снятия формы.
Чтобы при снятии формы пустотообразователи не прилипали к блоку и не затягивали за собой раствор, в них можно просверлить отверстия: по три диаметром 10 мм в каждом донышке пустотообразователя и по три диаметром 4-5 мм в одной боковой стенке каждого пустотообразователя прямо под верхней крышкой.
На формование одного блока уходит примерно около двух – трех минут, при условии, что керамзитобетонную смесь Вам будут замешивать, нагружать в ведра и подносить.
Для формования одного блока потребуется где-то около одиннадцати литров раствора.
Успешный предприниматель - не тот, кто все знает, а тот, который быстро учится.
|
|
| |
Semsey | Дата: Среда, 17.04.2013, 17:11 | Сообщение # 13 |
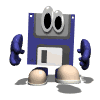 Admin
Группа: Администраторы
Сообщений: 309
Статус: Offline
| Для чего нужен пластификатор
Пластификаторы обеспечивают подвижность бетонных составов, в данном случае – керамзитобетона. Керамзитобетонная смесь с пластификатором имеет большую подвижность и заполняет форму для блока более плотно. Также значительно снижается расход воды для затворения смеси, от чего зависит наилучшее сохранение формы блока сразу после снятия с него виброформы. Применение пластификатора позволяет: увеличить подвижность керамзитобетонной смеси, что особенно актуально при формовании блоков:
снизить расход воды до 20-25% от первоначального объема при затворении смеси;
увеличить прочность готовых изделий более, чем на 20%, причем на любой стадии твердения, без увеличения расхода цемента;
исключить преждевременное схватывание и твердение керамзитобетонного состава:
снизить расход цемента до 25%, не теряя прочности готового изделия;
при изготовлении монолитных керамзитобетонных стен с внутренним армированием улучшить сцепление керамзитобетона и арматуры;
увеличить морозостойкость и трещиностойкость керамзитобетонных изделий – блоки получаются более плотными. Использование пластификатора позволяет снизить время вибрации при вибропрессовании блоков в 3-5 раз, что ускоряет сам процесс формования, соответственно снижается потребление электроэнергии и трудозатраты и увеличивается производительность. Исходя из этого - значительно повышается срок службы вибропрессовочных станков и снижаются затраты на их ремонт, что актуально при производстве больших объемов продукции. Улучшается поверхность изделий за счет уменьшения пористости. Альтернатива пластификаторам – обычное жидкое мыло или же моющее средство. Если добавлять его при замешивании керамзитобетонного состава – эффект будет такой же, как и при использовании пластификатора, изготовленного на предприятии. Подвижность смеси увеличится, расход воды снизится, преждевременного схватывания смеси происходить не будет. В данном случае, подвижность раствора будет зависеть напрямую от количества добавляемого моющего средства и соответственно от количества воды. Многие задаются вопросом: «А не будет ли качество блоков хуже при использовании мыла вместо пластификатора?». Здесь можно с уверенностью сказать – нет, не будет. Объяснить это можно тем, что для производства керамзитобетонных блоков используются простые составы пластификаторов, обеспечивающие только увеличение подвижности раствора. Более сложные, суперпластификаторы, способствующие более быстрому твердению или увеличению влагоотталкивающих свойств, используются в основном для производства железобетонных перекрытий и фундаментных блоков - они просто не востребованы при производстве керамзитобетона, ну а с функцией увеличения подвижности смеси вполне способно справиться и обычное жидкое мыло.
Успешный предприниматель - не тот, кто все знает, а тот, который быстро учится.
|
|
| |
Semsey | Дата: Среда, 17.04.2013, 17:14 | Сообщение # 14 |
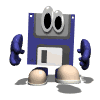 Admin
Группа: Администраторы
Сообщений: 309
Статус: Offline
| Проблемы при формовании
Почему форма плохо снимается с блока или вообще не снимается?
Причин этому может быть несколько.
1. Большее количество керамзитобетонной смеси, чем нужно для одного блока.
2. Слишком сухой раствор. Форма либо вообще не снимается, либо ломает блок, либо срывает углы.
3. Слишком мокрый раствор. Форму снять можно, но при снятии формы пустотообразователи засасывают за собой стенки блока. Блоки получаются бочкообразными, садятся по высоте, приобретают неправильную форму.
4. Отсутствие пластификатора. Керамзитобетонная смесь недостаточно подвижна для того, чтобы блок легко вышел из формы.
5. Использование крупного керамзита. Керамзит фракции 10-20 нельзя использовать для изготовления блоков, так как он препятствует равномерному распределению раствора в форме, вследствие чего блоки получаются рыхлыми. При вибропрессовании, крупный керамзит просто встает враспор между стенками формы и пустотообразователями, что сильно затрудняет снятие формы с блока.
6. Слишком много керамзита в керамзитобетонной смеси.
7. Использование карьерного песка. Карьерный песок более мелкий, нежели обогащенный. Раствор керамзитобетона, приготовленный с таким песком, слишком пластичен, что тоже не позволяет снять форму с блока без труда.
8. Остатки раствора на стенках формы и пустотообразователях после предыдущего формования. Форму для блоков нужно очищать от остатков раствора в конце каждого рабочего дня, а если не планируется делать блоки в течении продолжительного времени, то не лишним будет смазать форму машинным маслом и убрать в сухое место для хранения.
Почему срывает углы у блока?
1. Как уже говорилось выше – слишком сухой раствор или отсутствие пластификатора.
2. Мало цемента. Экономить на цементе нельзя – блоки получатся хрупкими, непрочными.
3. Бывает, что изначально приготовленная керамзитобетонная смесь имеет нужную консистенцию, но по истечении определенного времени, особенно в жару, она начинает подсыхать и схватываться. Можно в таком случае добавить немного воды и перемешать ее.
Почему блоки рассыпаются через несколько минут после формования?
1. Недостаточно цемента или пластификатора.
2. При формовании на одном большом поддоне, вибрация от формования блока передается на недавно отформованный, тем самым разрушая его.
Успешный предприниматель - не тот, кто все знает, а тот, который быстро учится.
|
|
| |
Semsey | Дата: Среда, 17.04.2013, 17:40 | Сообщение # 15 |
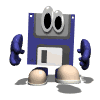 Admin
Группа: Администраторы
Сообщений: 309
Статус: Offline
| Себестоимость
Многие задаются вопросом: «Стоит ли производить керамзитоблоки самостоятельно и есть ли в этом какая-нибудь выгода? ». Попробую прояснить данную ситуацию. Рассчитать себестоимость одного керамзитобетонного блока вовсе не сложно.
Для начала нужно определить, сколько керамзитобетонной смеси потребуется для формования одного блока. Исходя из размеров формы для производства стандартного керамзитобетонного блока – это 390х190х190мм, соответственно 0.014 куба = 14 литров. Вычитаем из этого объема объем пустотообразователей, примерно 25-30%, получаем 0.010-0.011 куба, или 10 – 11 литров. Итак, с объемом керамзитобетонной смеси определились, попробуем рассчитать объем необходимых компонентов для ее приготовления.
Обогащенный песок. Расход песка на один блок – 0.005 куба = 5 литров.
Керамзит фракции 5-10мм. Керамзита потребуется тоже 0.005 куба = 5 литров.
Цемент. Цемент нужно брать марки 400, расход его составит порядка 1,25 кг на блок.
Воду, я думаю, учитывать не нужно. Моющее средство, в качестве пластификатора, тоже обойдется не очень дорого, да и расход его довольно мал, так что, можно не включать в себестоимость, хотя, на 3000 блоков у меня ушло примерно 50 бутылок объемом 0.5 литра стоимостью 8 рублей каждая – итого 400 рублей.
Теперь нужно определить, сколько же будут стоить эти 0.005 песка, 0.005 керамзита и 1.25 кг цемента.
Цены на обогащенный песок разнятся в различных регионах, да и продают его тоннами, а не кубометрами. Стандартно – один КАМАЗ 10 тонн примерно равен 7 кубам. Стоимость тонны обогащенного песка в нашем регионе – 400 рублей, следовательно, кубометр песка обходится в 571 рубль. Исходя из этого, определяем стоимость песка, затраченного на один блок – 3 рубля 40 копеек.
Керамзит фракции 5-10 стоит около 1100 рублей за куб, стало быть, 0.005 куба будет стоить 5рублей 50 копеек.
Мешок цемента (цена на 12.06.2012) 220 рублей, следовательно, 1,25 кг будет стоить 5 рублей 50 копеек.
Общая стоимость компонентов для одного блока составит 14 рублей 40 копеек, плюс затраты на электроэнергию, в принципе не столь существенные. Учитывая, что готовый керамзитоблок ( зачастую не заводского производства ) стоит сейчас порядка 36-38 рублей, есть смысл задуматься о производстве блоков своими руками.
Еще раз хочу обратить Ваше внимание на то, что цены на все компоненты в различных регионах довольно разные.
Еще одно, немаловажное замечание. Если керамзитобетонные блоки нужны Вам в небольшом количестве, порядка 300 – 500 штук, проще будет купить уже готовые блоки, нежели приобретать для их производства вибропрессовочный станок и бетоносмеситель. Если же речь идет о довольно большом количестве, 1000 и более штук – выгода будет ощутимой.
Успешный предприниматель - не тот, кто все знает, а тот, который быстро учится.
|
|
| |